Pricing for Profitability Requires Job Costing Accuracy
Looking Out for Pitfalls and Hidden Costs is Essential
Key Takeaways:
- Relying on outdated estimates or ignoring hidden costs can quietly erode your profit margins.
- Accurate job costing starts with real data, not gut instinct or wishful thinking.
- Communication between production and finance is essential to avoid costly surprises.
In today’s fiercely competitive manufacturing world, accurately understanding the true cost of production is essential for setting profitable prices. A timely, comprehensive and dependable job costing system ensures management can confidently base pricing decisions on reliable information.
Estimating Costs on New Products
Accurately estimating the cost of a product is important to meet the margin goals you have set for the finished product. But there are many pitfalls along the way, including:
- Basing cost solely on estimates arrive at before production. It is important to review your cost estimates AFTER production has begun to be sure all costs have been identified accurately. There may be unforeseen complexities encountered during production that can introduce invisible costs.
- Engineering problems encountered once production begins can tank the profitability of a product before it gets off the line. Resulting delays build intangible costs into the process if workers and equipment are idle while the problem is fixed. Make sure the engineering process is managed with efficiency in mind. Think “don’t recreate the wheel, just make the wheel perform as needed.” The product just needs to meet specifications. Each time you attempt to introduce a new, unproven technology into the production process, you risk exchanging profit for learning. Introduce new technology sparingly in a controlled manor. Proven processes produce profit.
- The job cost is based on your estimate, but you may find you didn’t do enough research. Thoroughly examine all the potential risks of cost overruns during production so you do not obliterate your profit through a lack of proper planning.
Underestimating or Overestimating Costs
Underestimating costs can happen in many ways. Failing to adequately research costs of parts and materials, forgetting to include labor and overhead costs or not using the right metrics and methods can all lead your job cost estimates astray.
Perhaps the most common mistake that leads to underestimating is simply wishful thinking.
You may want and expect your job costs to come in at a certain gross profit range. But if you haven’t looked at all the facts, you will run the danger of underestimating. Science and data always win over emotion, meaning a comprehensive analysis of all the parts, materials, processes, time, labor and overhead is critical to reaching a reasonably accurate job cost estimate.
Locking in pricing of parts and materials through long term contractual agreements (LTA) can help ensure accuracy in your job cost estimates, as well as hold the line on overall costs. Generally, the longer the term you are willing to commit to, or the higher the number of units you can commit to buy, the better your chances are of controlling prices. The best case is that the term of your LTA, matches the term of your customer contract.
Overestimating costs can be just as damaging as underestimating – and perhaps worse, since it may lead you to overprice the product and lose sales.
To avoid both underestimating and overestimating costs, make sure you understand the calculations, metrics and methods used to estimate job costs.
Sample Estimating Method
For instance, parametric estimating relies on statistical models and algorithms to predict project outcomes based on key characteristics or parameters.
How it works:
- Identify parameters: Determine the key characteristics or parameters that influence project costs, time or resources.
- Collect data: Gather historical data and statistical relationships between these parameters and project outcomes.
- Develop a model: Use the data to create a statistical model or algorithm that can predict project outcomes based on the identified parameters.
- Apply the model: Use the model to calculate estimates for new projects or project components.
Examples of parametric estimating might include estimating the cost of building a house based on the number of square feet, estimating the time it will take to complete a software project based on the number of lines of code or estimating the cost of a construction project based on the number of units or materials. In the case of building the house, you would identify each element of the home that needs to be constructed, such as the number of doors, windows, entryways, closets, bathrooms, drains, water supplies, walls, etc. A cost is then assigned to each element, multiplied by the number of occurrences of that element to arrive at the total cost of the house.
Hidden & Indirect Costs
All projects include hidden and indirect costs, some of which are accounted for by adding a standardized percentage to the cost estimate to account for overhead items such as utilities, maintenance, administrative support, taxes, insurance and other external costs that are essential for production. Costs of supplies and other consumables can accumulate over time. Overhead and consumable costs should be applied to each job.
Consider how you are capturing the direct costs of labor and equipment. Labor costs can change frequently as employees are given raises or are replaced by higher- or lower-paid workers. It is important to re-evaluate your cost of labor applied to a job each time raises are given to production employees. Have you factored in time for learning curves in your labor costs? Experienced machine operators work faster than trainees do, and the difference in productivity should be factored into the job cost estimate.
Other hidden costs include:
- Transportation and freight, inbound or outbound.
- Idle time costs, for instance, as machines wait for the next step or a quality review.
- The cost of scrap. The more complex the production, the higher the risk of scrap, which needs to be added to cost. Estimating costs for a fairly complex product requires using a higher scrap rate. Underestimating the impact of scrap is a common issue affecting profit in manufacturing.
- Changing market conditions, such as tariffs or limits on supply of a key manufacturing component.
- Scope changes. If the scope of a job changes – for instance, the number of units needed is greater or less than originally anticipated, potentially leaving you with more material than you need or worse, less than you need to complete the contract. If during the engineering phase, a part that wasn’t included in the original estimate is found to be needed, the cost estimate must be revised, which will impact the anticipated price of the end product or if the contract is locked, results potentially in a loss on the product.
By using science and data to build cost estimates, you take the human element out of the process and ensure higher levels of accuracy. This will show up in the gross profit margin, particularly if each product line is accounted for separately, yielding accurate information on costs and revenues.
Analyzing Spikes & Dips in the Financials
If spikes or dips appear in the month-to-month gross profit results, they may indicate anomalies in the cost estimating. Perhaps someone forgot to order certain materials needed for production, so they had to be purchased on the spot market at 25% above the contract price. Or a high-speed production machine may have broken down and the units had to be produced on a slower machine. Or maybe production is behind schedule, and you were forced to pay excess overtime.
Deviations in the production process will happen that throw off cost estimates. The key is to find out why they happened and put guardrails in place (Root Cause, Corrective Action), so they aren’t repeated. Order the correct quantity of materials far enough in advance to avoid a costly emergency purchase. Make sure regular maintenance is done on all machinery so production is not hindered. Check production levels on a weekly or daily basis to make sure you can meet deadlines without incurring overtime costs.
Close communication between the accounting and finance department and the operations/production people is crucial for proper cost oversight.
Questions?
Accuracy in cost estimating is key to setting profitable prices on products and protecting gross profit margins. But hidden costs and other pitfalls can throw even the most careful cost estimates off track.
If you would like a job cost review to help strengthen your cost estimating process, contact an Adams Brown manufacturing accountant.
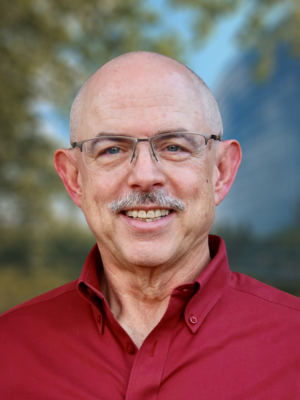