Supply Chain Disruptions Challenge Midwest Manufacturers
Problem Has Shifted to Logistics
Supply chain disruptions primarily caused by the COVID-19 pandemic are presenting major challenges for Midwestern manufacturers, and the resulting shortages of raw materials and components are likely to continue indefinitely.
Until the pandemic subsides enough for suppliers worldwide to ramp up production to fill back orders, U.S. manufacturers need to focus on finding alternative vendors and even reconfiguring their production processes to keep their products moving.
Logistics Bottleneck
The supply chain disruptions have been significant worldwide since the beginning of the pandemic more than one year ago, but now as producers are getting back to work and filling backlogged demand, the slowdown has shifted to the logistics end with strained capacity common to seaborn shippers, air shippers and freight trucking companies. Bottlenecks at coastal ports in the U.S., in part due to capacity constraints and in part due to COVID-19 outbreaks among dock workers, are exacerbating the problem.
The supply chain problems are hitting manufacturers across the board, with many reporting difficulties in finalizing their production and fulfilling customer orders. In some cases, they may have enough components and raw materials to take them 90% of the way through the production process but they are lacking one or two critical components needed to finish the job.
Relationships with customers, vendors and workers are being impacted by the supply chain disruptions. Delayed fulfillment of orders makes it critical for manufacturers to communicate often with customers to keep them informed. Longstanding relationships with vendors are being tested as many manufacturers turn to alternative suppliers. And workers are being asked to be flexible as production schedules are changed to accommodate the ebb and flow of components and raw materials.
Price increases among raw materials and logistics – particularly trucking costs – are another impact of the supply chain problem.
What to Do?
We recommend that manufacturers who are experiencing supply chain disruptions take several measures to maintain relationships and keep their production lines moving as closely as possible to normal capacity:
- Constantly communicate with your vendors. Get updated timeframes and delivery dates and keep yourself at the forefront of the vendor’s mind.
- Likewise with customers, communicate often, keeping them informed of delays and, as much as possible, giving them concrete commitments for delivery.
- Be flexible and proactive with your production scheduling. Create several scenarios and update production day by day, depending on what components and raw materials are scheduled to arrive. If one item comes in but not another, respond to that by scheduling around the missing item. Manufacturers that have automated scheduling systems have an easier time running what-if scenarios.
- Look for alternative supply chains. Even if it helps you finish only part of your goods, it keeps you moving. If there is an alternative component you can use, consider that.
- Consider seeking logistics company alternatives. Many manufacturers tend to stick with the same logistics company, but this may be the time to see if someone else can help fulfill your needs. If a customer needs delivery of your product immediately and your shipper can’t get to it for a week, look around.
Silver Lining
Because many companies have had to seek alternative sources for their goods during the pandemic, many manufacturers have seen a significant increase in e-commerce sales, which has impacted logistics. They’re selling to new customers they’ve never worked with, and they’re shipping goods farther than they have traditionally. Getting new business is a good thing, but it also puts pressure on the manufacturers.
Despite the supply chain and logistics challenges, now is the time to solidify the relationships with those new customers. You want them to stick with you when the pandemic is behind us.
If you have questions about how your company can deal with supply chain disruptions, contact your Adams Brown advisor.
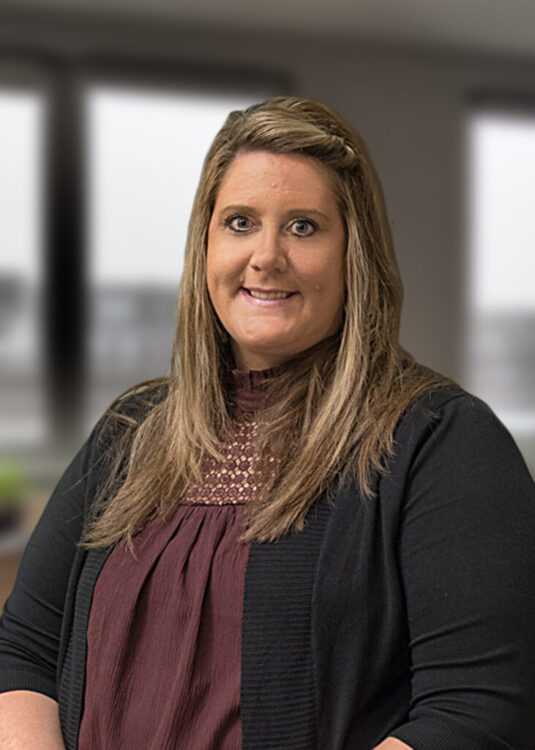